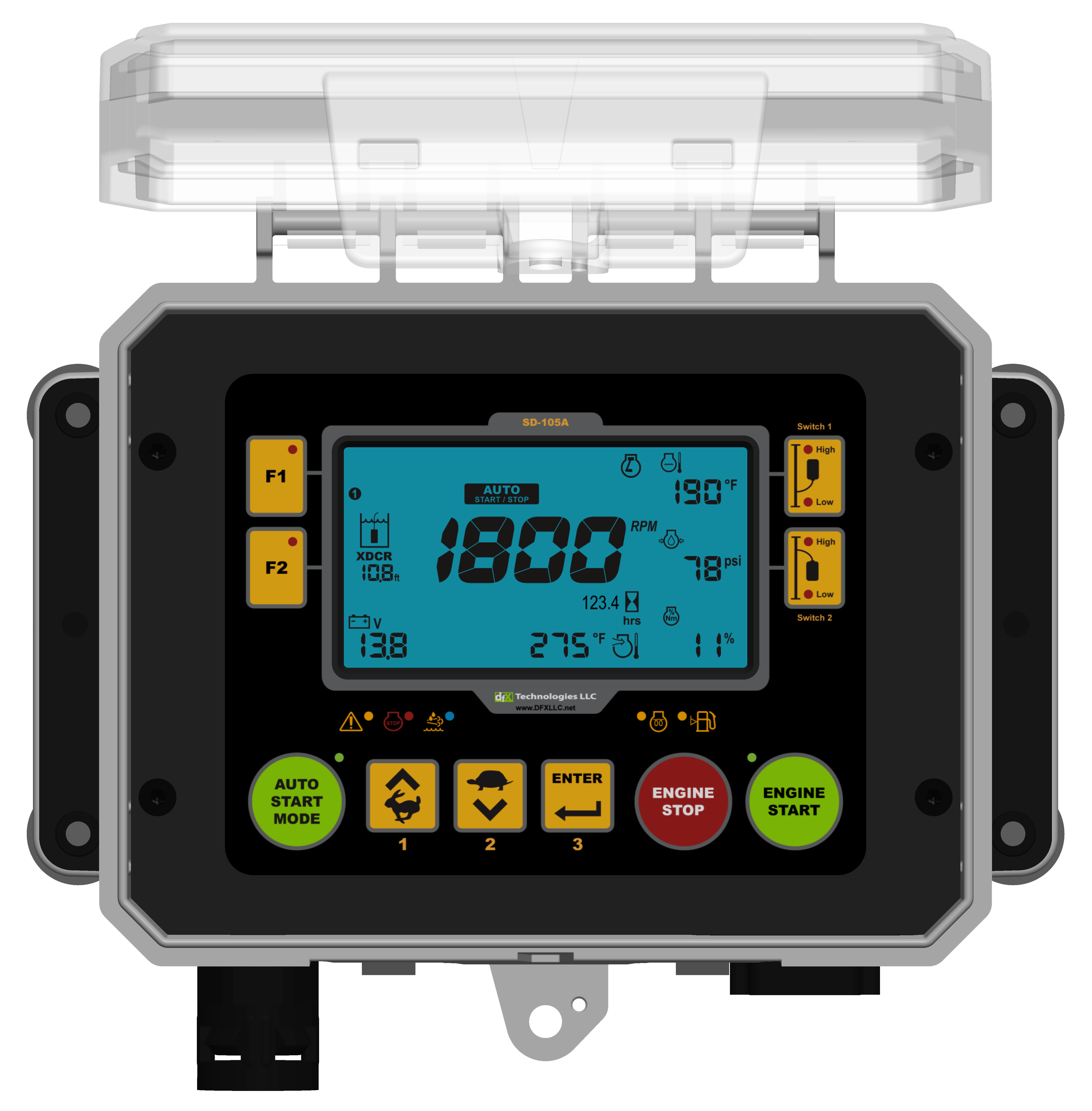
SD-105AP Automatic Engine Start / Stop Controller NEMA 4x Enclosure
SD-105AP NEMA 4x Panel Solutions
DFX’s SD-105AP series controllers housed inside a 8″x6″x3″ NEMA 4x Polycarbonate enclosures are designed for the diesel-powered market needing automatic engine start/stop. The SD-105A which was originally designed for the dewatering market includes built in I/O and can automatically start and stop the engine via one or two switches or a 4-20 mA pressure transducer or a combination of floats and transducers. The auto throttling capabilities of the SD-105AP in combination with the transducer automatically adjusts engine RPM to maintain a desired water level which make the equipment more reliable and helps increase fuel economy. Switch status is indicated via bright LEDs on the panel membrane. All engine parameters, sensors values, switch states and mode state are displayed on the CANbus J1939 network making the SD-105A ideal for telemetry systems for monitoring critical applications.
Automatic Engine Start/ Stop Features
- NEMA 4x polycarbonate enclosure with isolation mounts can be customized with waterproof I/O connectors from 4-pos to up to 12-pos
- Password protected auto and manual modes requires a pass code pin before controllers start mode can be changed which helps protect against unauthorized people from disabling the auto start mode or starting the equipment.
- Compatible with one float, two floats, pressure transducer or a combination of pressure transducer and two float switches.
- Empty and fill modes are not dictated by the float switch type. The SD-105A can use any float switch type (Normally Open or Normally Closed) for both empty and fill modes.
- Bright LED lights on the membrane indicates a quick visual reference displaying float switch status.
- Auto start/stop parameters can be easily changed via separate passcode pin protect pin menu system.
- Pressure transducer values are indicated on the XDCR LCD display parameter in either a percentage or in level length (feet/meters).
- Low standby current
Standard Features and Benefits
Immediate boot up time
Keyless engine start/stop with optional PIN number protection.
Up to 2 membrane switches with red indicator LEDs for accessory control.
Designed for J1939 electronic engines.
Optically bonded sun light readable segmented LCD display
RGB LCD backlight supports multiple colors.
Controller installs into 118.5 mm by 154.62 mm (4.665” by 6.087”) panel opening using provided mounting hardware.
Field configurable and programmable
DPF regeneration control capabilities
Resettable service timer
Engine monitoring and diagnostics with text descriptions for select SPN and FMI codes.
Simple plug-and-play installation customized to the specific application allows rapid equipment completion.
Versatile design enables customization for customer’s specific applications.
Optional wireless remote control connects to the secondary M12A connector that allows both start/stop and remote throttle operation.
Specifications
NEMA 4x enclosure size: 8″x6″x3″
Operating voltage: 8 to 30 VDC
Standby current: 30 mA
Operating current: 190 mA
LCD heater current: less than 850 mA
Operating temperature: -40° to 176° F (-40° to 80° C)
Waterproof potted design front and back
Reverse polarity protection
2-year limited warranty
Solid State I/O
I/O Connector Options
M12A Circular Connectors
- Primary M12A connector for SAE J1939 (CANbus 2.0B)
- Secondary M12A connector for SAE J1939 (CANbus 2.0B) or RS-485 (optional) with programmable power control option
DT-12-Pos Connector
- Battery power
- Ground (3)
- SAE J1939 (CANbus 2.0B) or RS-485 (optional)
- 4-20 mA, 0 to 5V (option) or 0 to battery (option) transducer input
- Transducer power
- Switch inputs for automatic start/stop operation (2)
- High side driver
- Low side driver
DT-6 connector (optional)
- Digital switch inputs (4)
- High side driver
- Ground
Modbus RTU RS-485 (optional)
All SD-105 displays support optional Modbus RTU via the optional RS-485 interface.
NEMA 4x Enclosures Options
There are many engine applications that require an enclosure around the display for extra protection. NEMA 4x polycarbonate enclosures with clear lockable protective cover are available for our display products. These plug and play panels have the wire entry at the bottom of the enclosure and includes 4 vibration isolators mounted in sheer. Each enclosure can also be customized with additional I/O connectors and is available with a lockable latch integrated in the lid or with a stainless-steel metal latch.
Integrated Latch On Door Stainless Steel Latch
Available I/O connectors
12-Pos DT Series Connector 6-Pos DT Series Connector 8-Pos DT Series Connector 4-Pos Ecomate Connector with Cap
The DFX Controller Concept
We reinvented engine control for off-highway equipment by creating a simple modular plug and play system that reduces cost, simplifies installation, and increases control capabilities. Our unique system consists of our AE-120 engine controller I/O module, a standardized plug and play engine harness, a simplified single M12A cable extension harness, and our family of display products. This system is designed for applications from simple manual engine start/stop to sophisticated automatic engine start/stop with integrated I/O or utilizing our CANbus J1939modular general purpose I/O module or custom keypads for adding more capabilities.
DFX’s SD-65 and SD-105 series CANbus based HMI displays utilize an optically bonded segmented LCD which high contrast is extremely readable even in direct sunlight, has instantaneous bootup time, and has an operating temperature of -40° to +80° C (-40° to 176° F). The displays are embedded inside a heavy-duty low-profile CNC machined aluminum housing and is available in multiple sizes, with optional function keypads, custom NEMA enclosures or a dash mount option which can be integrated into customer equipment.
DFX Display HMI Advantages:
- Extremely readable in direct sunlight
- Heavy duty optical bonded LCD cover glass with antiglare coating
- Instantaneous bootup time allows for fast starts.
- Designed for industrial application.
- Interfaces to our AE-120 engine controller with a single M12A cable
- Display engine fault code in plain text
- RGB backlight allows the backlight color to be configured.
- Standard LCD heater for cold climate conditions
- Keyless engine control with simple passcode protection
- Tier 5 compatible with regen
- Manual or automatic engine start/stop operation
- Hardware and software customizable at additional cost
Keyless Engine Start Lockout with PIN Protection
Having a mechanical key switch on your engine can be problematic if the key is lost, stolen or broken which can lead to expensive downtime. The new standard at DFX is KEYLESS which helps alleviate this problem. Simply press any button on the controller to wake up the system, press the start button and follow the LCD prompts to enter the PIN. For our SD-105A automatic engine start/stop applications a PIN is also requires enabling and disable automatic engine start/stop mode.
Customers who want a mechanical key switch can utilizes our optional software app in combination with the I/O inputs on the AE-120 to enable a mechanical key switch.
Throttle Control
DXF controllers use TSC1 (also called CANbus throttling) to support multiple throttle types which can be easily configured via the controllers integrated menu system. Engine speed is software controlled utilizing only the rabbit and turtle buttons on the controller’s membrane.
Supported Throttle Types
- Variable Speed
- 2-State Throttle
- 3-State Throttle
- 4-State Throttle
- Constant Speed
The default variable throttle uses the rabbit and turtle switches to adjust the desired speed between idle and the maximum programmed engine speed. The engine returns to idle on the next restart.
2-state, 3-state and 4-state throttle configuration uses up to four customer defined preset RPMs. Pressing the rabbit button selects the next higher preset and the turtle button selects the next lower preset. Constant speed runs the engine at a customer defined preset RPM.
Each controller auto detects TSC1 commands from an external device and disables conflicting messages from the controller. This eliminates problems that can occur when multiple TSC1 messages are sent and avoids having to manually disable the throttle function in the controller.
Function Keypad and Custom Membrane Graphics
Applications needed the ability to turn on and off optional auxiliary devices can use the SD-105 display module which supports up to four software-controlled function buttons. The function keypads are CANbus J1939 based and together with displays I/O or our optional AE-220 general purpose I/O module can turn on and off auxiliary outputs. Each function key be custom programmed as either latching, momentary or with an on-delay or off-delay timing function. Since our integrated keypads are CANbus based our function buttons could also be used to control engine functions such as custom RPM setting, activating engine cooldown, canceling engine cooldown or any other customer specific requirement. Each function key includes a bright red LED which indicates when function button is active. The standard SD-105 display buttons are marked with a generic F1, F2, F3 and F4, however custom graphics can be made available to the exact requirement of the customer with a one-time engineering fee and an annual commitment of 100 units.
STANDARD GENERIC KEYPAD GRAPHICS EXAMPLE CUSTOM KEYPAD GRAPHICS
AE-120 Engine Controller I/O Module
Typically the engine control function is embedded in the main controller. DFX designed our unique system so that the engine I/O module and display HMI are separate devices connected by a standard M12A cable. This smart concept keeps the high-power requirements at the engine where the power is needed with a standardized short engine interface harness. This concept eliminates having expensive extension or custom engine harnesses.
The AE-120 is a microprocessor controlled I/O module that mounts at the engine and controls ECU power, starter motor, alternator excitation and ignition accessory power. The AE-120 is also equipped with 3 inputs which can be configured for most fuel level sensors, auxiliary shutdown inputs or even as analog inputs for custom sensor requirements. Each AE-120 is equipped with a M12A connector that allows the use of our low cost CANbus J1939 extension cables with over molded IP67 connectors which can be extended up to 100 feet away from the engine.
AE-120 Advantages
- Heavy-duty sealed I/O module housed inside a CNC machined aluminum housing
- Controller mounts at the engine keeping the high power at the engine where the power is needed
- Simplifies the wiring by standardizing the engine wire harness to a simple design that can meet most applications
- Simplified the panel wiring using a single M12A CANbus J1939 cable easily modified to the desired length
- 4 high-power solid-state outputs
- 3 digital or analog inputs
- Built in starter motor and over crack protection
- Can be configured with an engine pre-start alarm
- Module can be customized to meet specific requirements
Power Box with Integrated CM-120 Engine Controller
Our CM-120 is our OEM solution for the engine control module. We have worked closely together with OEMs and engine manufacturers who require an ECU power management system. Our team then developed a power box concept with high power relays, an array of fuses, CANbus diagnostic connector with our integrated CM-120 engine controller embedded directly into the power box. Our power box design includes our standard M12A connector display interface creating a plug and play system.
Stock M12A Extension Cables
Our low cost over molded IP 67 M12A connectors, Includes CANbus J1939 and power and ground inside a heavy-duty PVC coated cable.
111-0021-1000 |
5-Pos M12A CANbus Power Extension Female 90 to Female Straight |
1 m (39“) |
111-0021-3000 |
5-Pos M12A CANbus Power Extension Female 90 to Female Straight |
3 m (118”) |
111-0021-5000 |
5-Pos M12A CANbus Power Extension Female 90 to Female Straight |
5 m (197”) |
111-0021-7620 |
5-Pos M12A CANbus Power Extension Female 90 to Female Straight |
7.5 m (300”) |
Customer cables available on special request
General Purpose I/O Module
Our AE-220 general purpose I/O module is an optional add-on CANbus J1939 controller for applications requiring more complex monitoring and control of the engine and equipment functions. This I/O module connects to the CANbus J1939 network via our plug and play M12A cables and includes separate high power and ground pins for providing power to sensors, valves, actuators, etc. The AE-220 can support high level devices such as tachometer, quadrature encoders, differential pressure senders, pressure transducers, flow meters, actuators, and PWM Valves. The AE-220 CNC machined aluminum sealed housing drops into panel mount opening. Since the AE-220 is CANbus based the device digital outputs signals can be activated from the SD-105 display function keypad or our optional KP series keypads.
FEATURES
General purpose I/O module adds additional capabilities to the standard I/O configured display when applications require more complex monitoring and control.
The AE-220 has two CANbus J1939 ports and easily connects to the CAN network via our M12A plug and play cables.
Can be configured to control DC powered linear actuators or electric motors.
Module supports:
-
- Up to 8x digital pins. Each digital pin can be configured as an input or a 1A power output. A custom hardware stuffing option is available for applications needing up to 7A on each pin.
- Up to 2x analog pins (4-2mA, 0-5V, 0-30V)
Heavy-duty weather-proof design utilizes high quality sealed connectors.
Modular design allows the AE-220 to be installed near sensors, actuators, hydraulic valves etc. which helps simplify wiring and can also reduce electrical interference.
Plug and Play Remote Control
![]() |
An optional CANbus J1939 based wireless remote-control system is available for applications needing to control an engine up to 1000 ft away from the engine. The base receiver connects directly into the second M12A CANbus connector on any SD series display. Our standard remote-control allows engine remote start/stop, RPM throttle control. Optional functions allow the operator to controller up to two additional outputs. Features
|
Software
When you choose DFX Technologies for your engine and equipment control provider you’re not getting a generic product. Each DFX product is custom engineered for around the application. Our knowledgeable team of engineers carefully evaluation each requirement and we then provide a turnkey solution. Having the ability to customize our software is a great benefit of working with DFX Technologies. We have invested many years to develop our software kernel which was carefully designed around our complete product line. Having this base software design that is compatible with all DFX products gives us the ability to easy develop custom apps that can add features and capabilities to our product line.
Available Software Apps
- Dewatering automatic engine start/stop
- Water jetting which controls RPM to a desired PSI using a 0-5V pressure transducer
- Automatic TSC1 auto detect (Standard on all DFX controllers)
- Engine start stop via mechanical key switch or toggle switch.
- Plug and play remote control capabilities (Standard on all DFX Controllers)
Configuration Software
Our Windows® PC configuration tool allows our customer to configure each controller to their exact requirement. Using a simple USB dongle connecting to the M12A connector allows quick and easy customization. This simple to use software allows standardizing configurations and quickly customizing how the DFX system works.
SD-105P Engine Controller NEMA 4x Enclosure
Features and Benefits
• Immediate boot up time
• Keyless engine start/stop with optional PIN number protection
• Automatic start/stop operation via switch and/or transducer inputs (automatic start/stop option)
• Up to 4 membrane switches with red indicator LEDs for accessory control
• Designed for J1939 electronic engines
• Optically bonded sun light readable segmented LCD display
• RGB LCD backlight supports multiple colors
• Controller installs into 118.5 mm by 154.62 mm (4.665” by 6.087”) panel opening using provided mounting hardware
• Field configurable and programmable
• DPF regeneration control capabilities
• Resettable service timer
• Engine monitoring and diagnostics with text descriptions for select SPN and FMI codes
• Simple plug-and-play installation customized to the specific application allows rapid equipment completion
• Versatile design enables customization for customer’s specific applications
• Optional wireless remote control connects to the secondary M12A connector that allows both start/stop and remote throttle operation
Specifications
• Operating voltage: 8 to 30 VDC
• Standby current: 30 mA
• Operating current: 190 mA
• LCD heater current: less than 850 mA
• Operating temperature: -40° to 176° F (-40° to 80° C)
• Waterproof potted design front and back
• Reverse polarity protection
• 2-year limited warranty
Solid State I/O
• DT-12 Connector
o Battery power
o Ground (3)
o SAE J1939 (CANbus 2.0B) or RS-485 (optional)
o 4-20 mA, 0 to 5V (option) or 0 to battery (option) transducer input
o Transducer power
o Switch inputs for automatic start/stop operation (2)
o High side driver
o Low side driver
• DT-6 connector (optional)
o Digital switch inputs (4)
o High side driver
o Ground
• Primary M12A connector for SAE J1939 (CANbus 2.0B)
• Secondary M12A connector for SAE J1939 (CANbus 2.0B) or RS-485 (optional) with programmable power control option
SD-65N Engine Controller in NEMA 4x Enclosure
The SD-65N is DFX’s entry level engine controller for electronically controlled J1939 engines. This compact controller fits inside a 4″x4″x 3″ NEMA 4x Waterproof enclosure or dash mount utilizing a rear mounting bracket. The SD-65N has larger buttons and includes an I/O connector when applications has custom requirements. The SD-65N is ideal for smaller engines; however, has technology to easily control larger more sophisticated engines.
The sunlight readable LCD is optically bonded with an anti-glare coated strengthened glass for optimal clarity and durability. The SD-65N LCD display uses both segmented liquid crystal and dot-matrix technologies. LCD displays engine parameters, fault codes as well as plan text descriptions for menu descriptions, engine fault codes and the ability to display custom parameters. Each LCD display is equipped with RGB backlight LEDs for night vision. LED backlight color can be easily configured via the menu system to the customer preference.
The SD-65N unique modular design simples wiring by utilizing a single CANbus extension cables with M12A waterproof connectors. These plug and play cables consist of a power, ground and shielded CANbus J1939 wires which can be extended up to 100 meters away from the engine. When utilizing our splitter connectors adding additional CANbus based products such as I/O module modules, audio buzzers, keypads, wireless remote control or even telemetry modules an easy task.